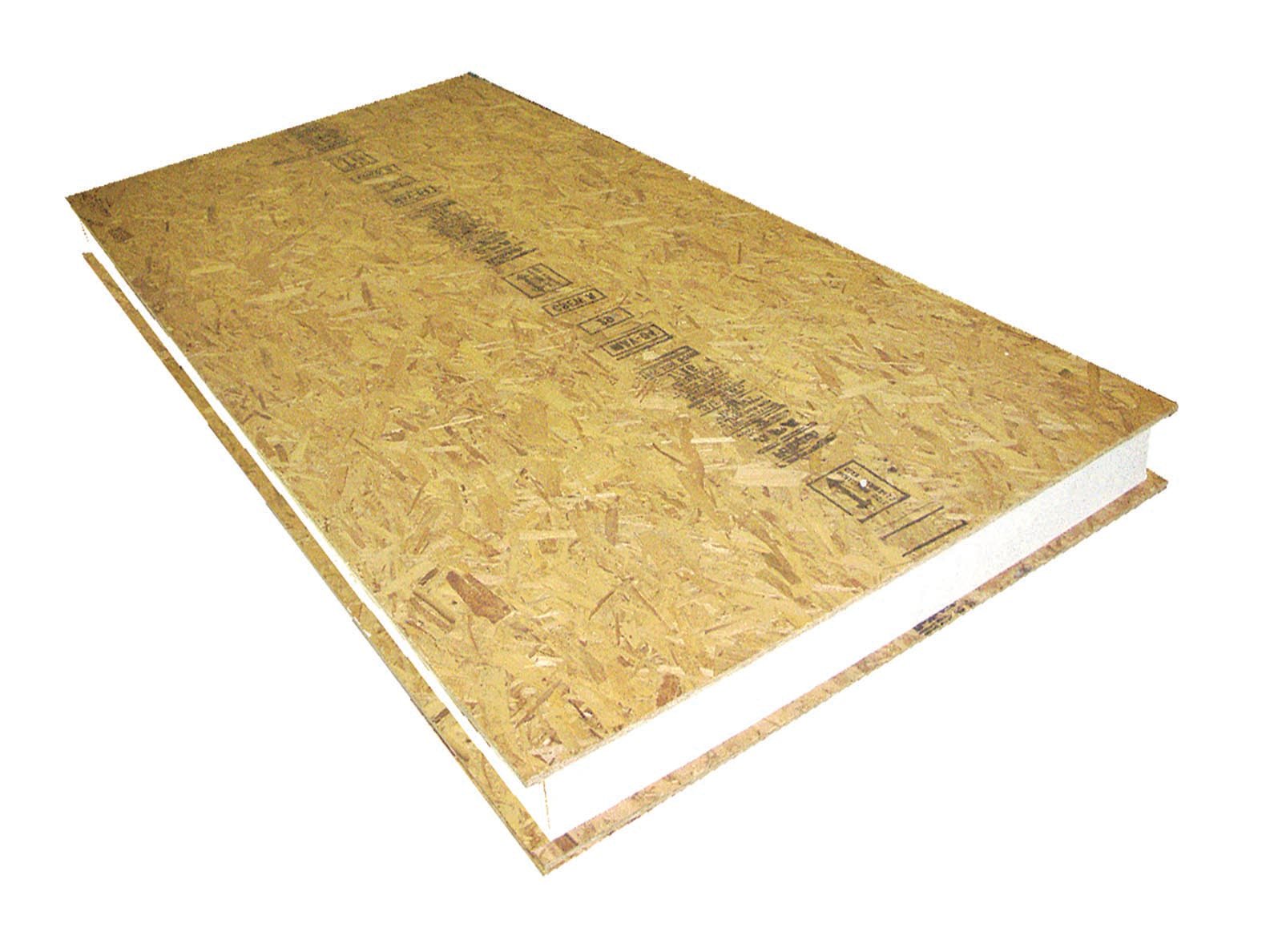
Why Structural Insulated Panels?
PorterSIPs is a single source provider of ready-to-assemble insulated building shells. These turnkey solutions can vary in scope and include not just the SIPs, but additional features such as truss packages and insulation. Improve your critical path with a complete PorterSIPs envelope
- Home
- Why Choose Us
Jump to section
PorterSIPs Advantage
PorterSIPs are the key to faster construction and energy efficiency.
- SIP buildings use up to half the energy of conventional construction.
- SIPs can be used on most building designs and are particularly useful in open designs with long roof spans.
- SIPs can be erected 300% faster than conventional buildings.
- SIPs are designed and engineered to meet required loads and are inherently stronger than conventional framing.
- SIP buildings have less interior noise, fewer drafts, and more consistent interior temperatures.
- SIP buildings have better control of air quality due to their inherent air-tightness.
- Building with SIPs helps earn LEED points.
- PorterSIPS licensed in-house engineering team provides reliable and quick, fully-engineered submittals and calculations.
PorterSIPs Difference
Fast Construction
- Weeks less than general construction
- Earlier occupancy
- Combined structure & insulation
- Precision CNC manufactured panels
- Improves prototypical efficiencies
- Reduces structural supports
- Up to 24' clear spans
Cost Saving
- Reduces operating costs
- Up to 50% more energy efficient
- Improves critical path timeline
- Eliminates construction trades
- Factory provided installation
- Single source building envelope
- Requires less structural support
- Shell project management provided
Environmentally Friendly
- Contributes to LEED certification
- Eliminates SIPs job site waste
- Reduces landfill costs
- Exceeds code requirements
- Airtight construction
- Superior R-values
- Reduces HVAC size requirements
- Improves HERS rating*
- Fewer steps for energy requirements
- Environmental Product Declaration
EPD Statement Available. *Home Energy Rating System
Single Source Provider
Structural Insulated Panels
Insulating layer of rigid EPS (Expanded Polystyrene) sandwiched between two layers of OSB (Oriented Strand Board). SIPs are a unique building product that combines structure and insulation in one large rigid panel.
-
Provide & Install:
Wood truss, steel joists, columns, beams, headers, purlins & girts
Roofing
Framing (Interior walls, dormers, bump outs, parapets, all plating, windows, door rough framing, and headers over framing)
-
- Engineered shell
- Sealed engineering drawings
- Sealed engineering calculations
- Code listed
- Additional engineering services
- 3D model CAD drawings
-
- Manufacturer supplied installation
- Union/non-union labor
- Servicing North America
- Efficient & fast installation crews
- Insured and bonded
Repeatable Construction
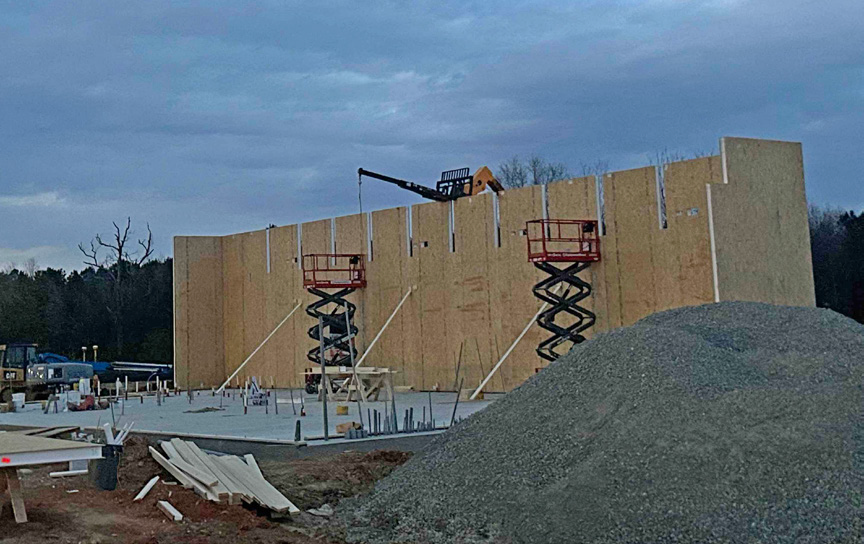
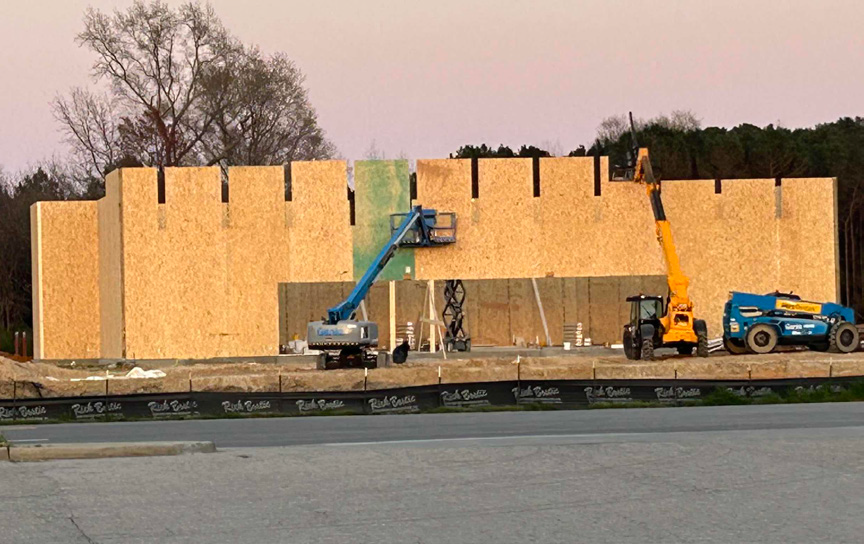
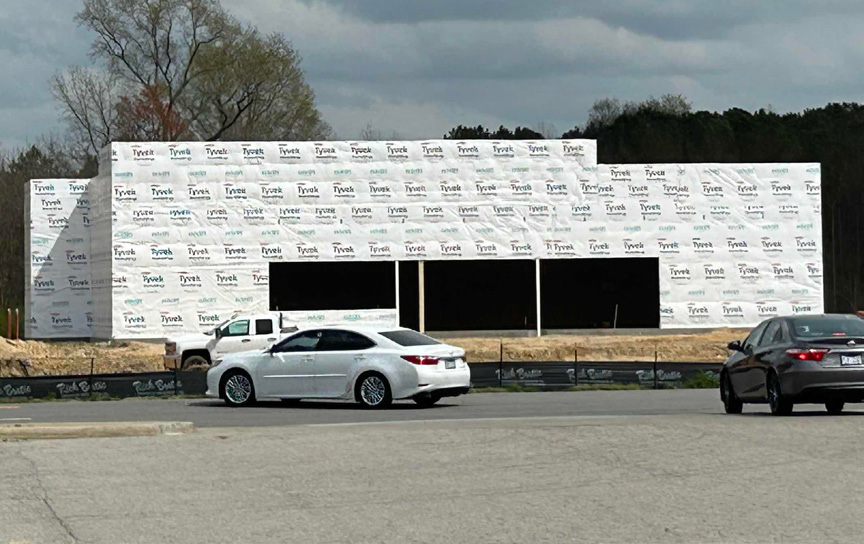
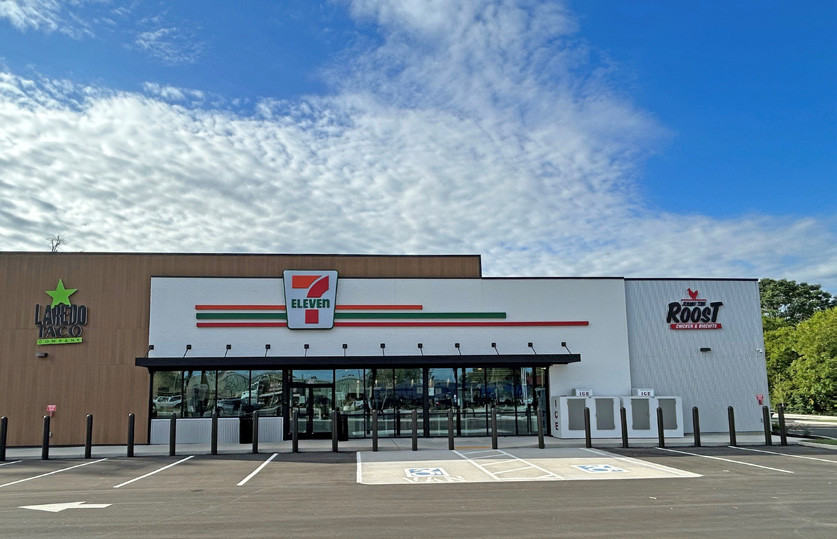
How PorterSIPs Work
SIPs share the same structural concept as an I-beam or I-column. The rigid EPS core of the SIP acts as the web, while the OSB sheathing exhibits the same function as the flanges. SIPs combine several components of conventional building, such as studs, rafters or joists, insulation, vapor barrier and air barrier. They can be used for many different applications, such as exterior walls, roofs, and floor systems.
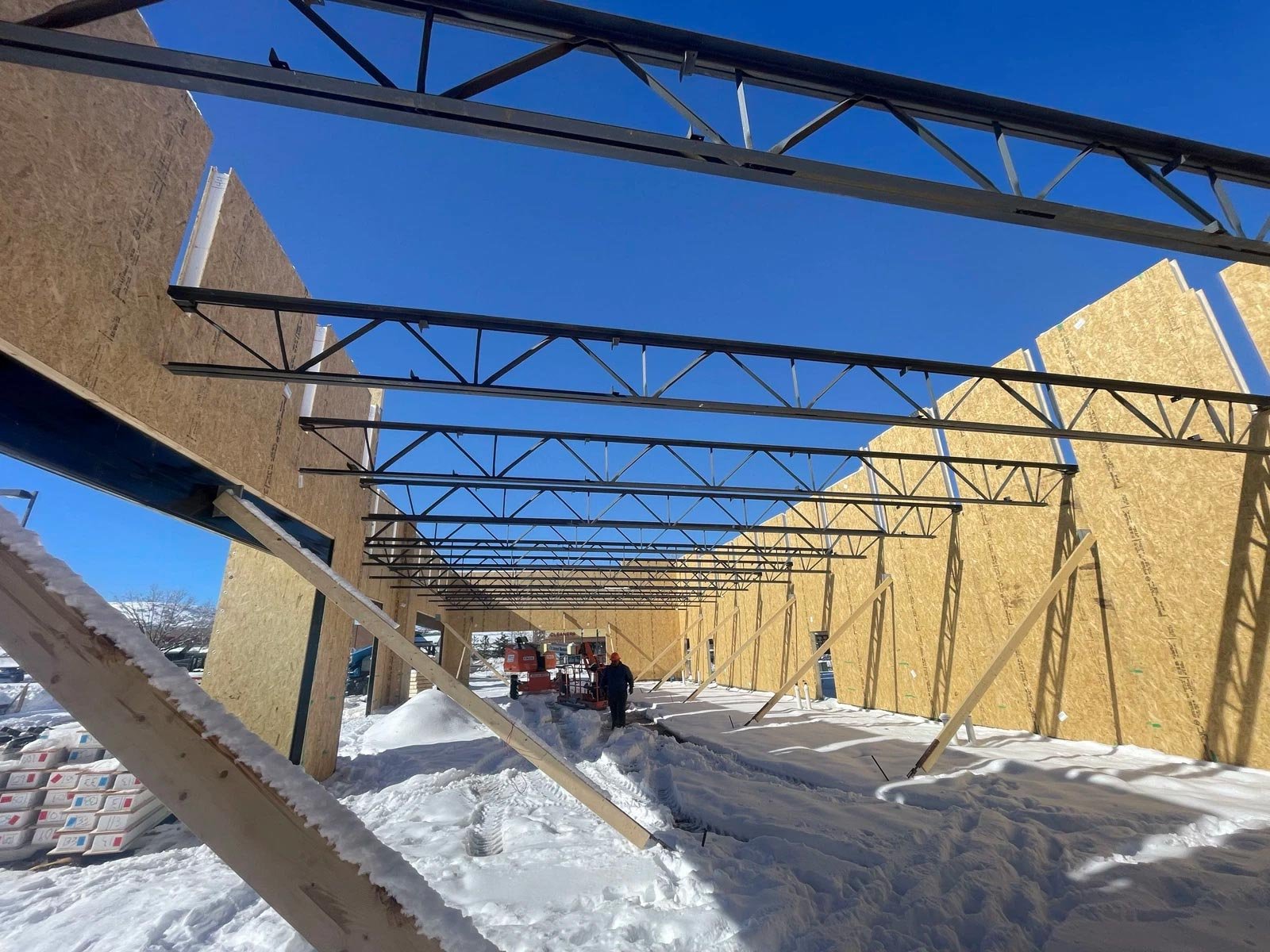
The key to PorterSIPs performance is that the EPS foam core keeps the OSB skins from buckling by keeping them “in plane”. The rigid plastic foam core of expanded polystyrene (EPS) is the insulation and the web of the “I” beam. The thicker the panel, the more load the panel will carry and the greater the insulation value.
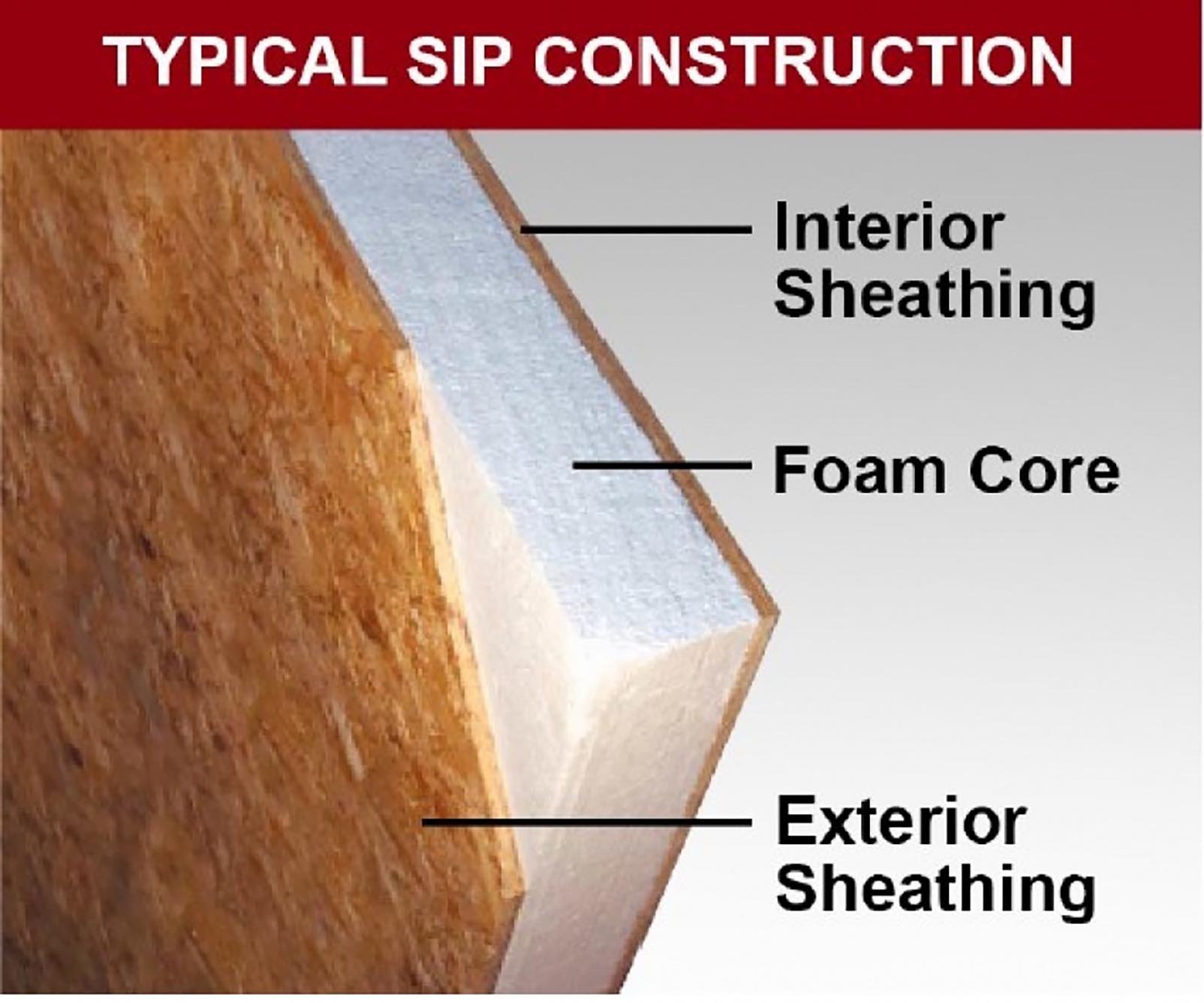
PorterSIPs use CNC cutting for ease of assembly. Our 3D parametric modeling techniques ensure an accurate accounting for all panels and their connections. Final SIP cutting is done on our state-of-the-art Hundegger so field cutting is typically not necessary allowing rapid, accurate, and reliable delivery.
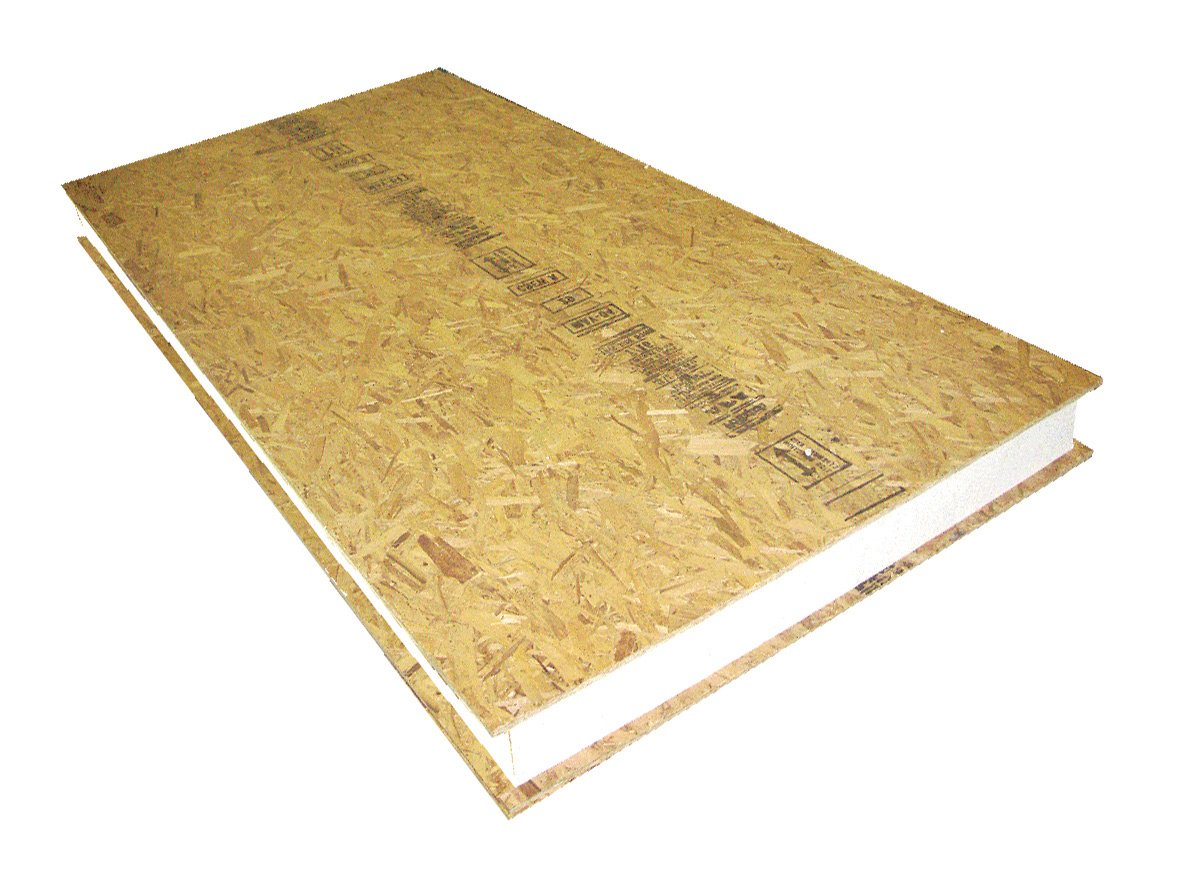
SIPs are an evolution of stick-built construction and a hybrid that uses dimensional lumber for corner connections, plates and window/door framing point loads, and sub-fascia. SIPs are sized to work with standard dimensional lumber and eliminate many steps saving both time & money. SIPs contain the “framing”, sheathing, and insulation in a product that is assembled in one step.
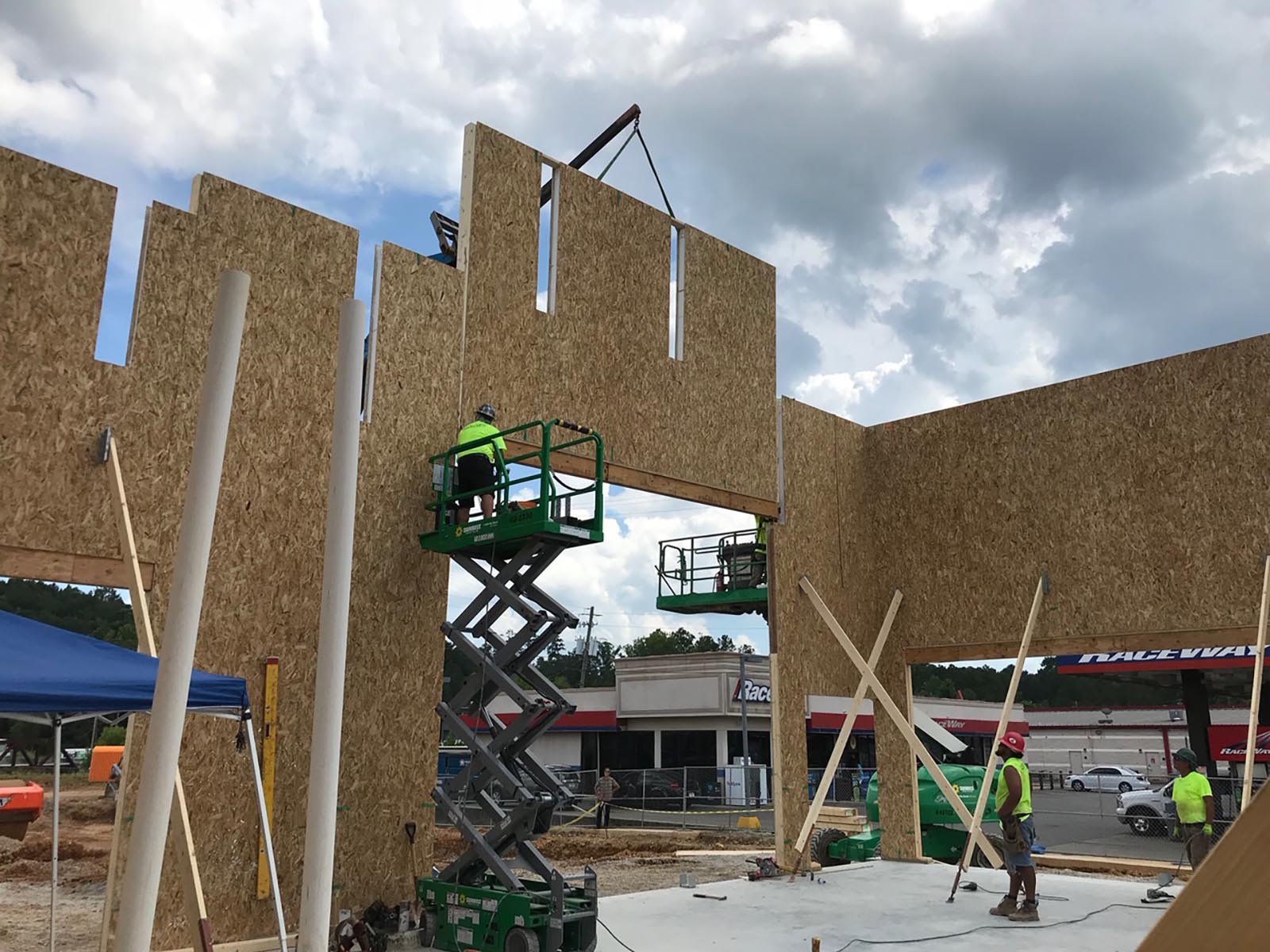
Jumbo SIP panels are available in 8’x24’ sheets. These large panels are a big design advantage and allow rapid assembly with fewer parts. With fewer joints, the building is stronger and requires less support of load bearing walls.
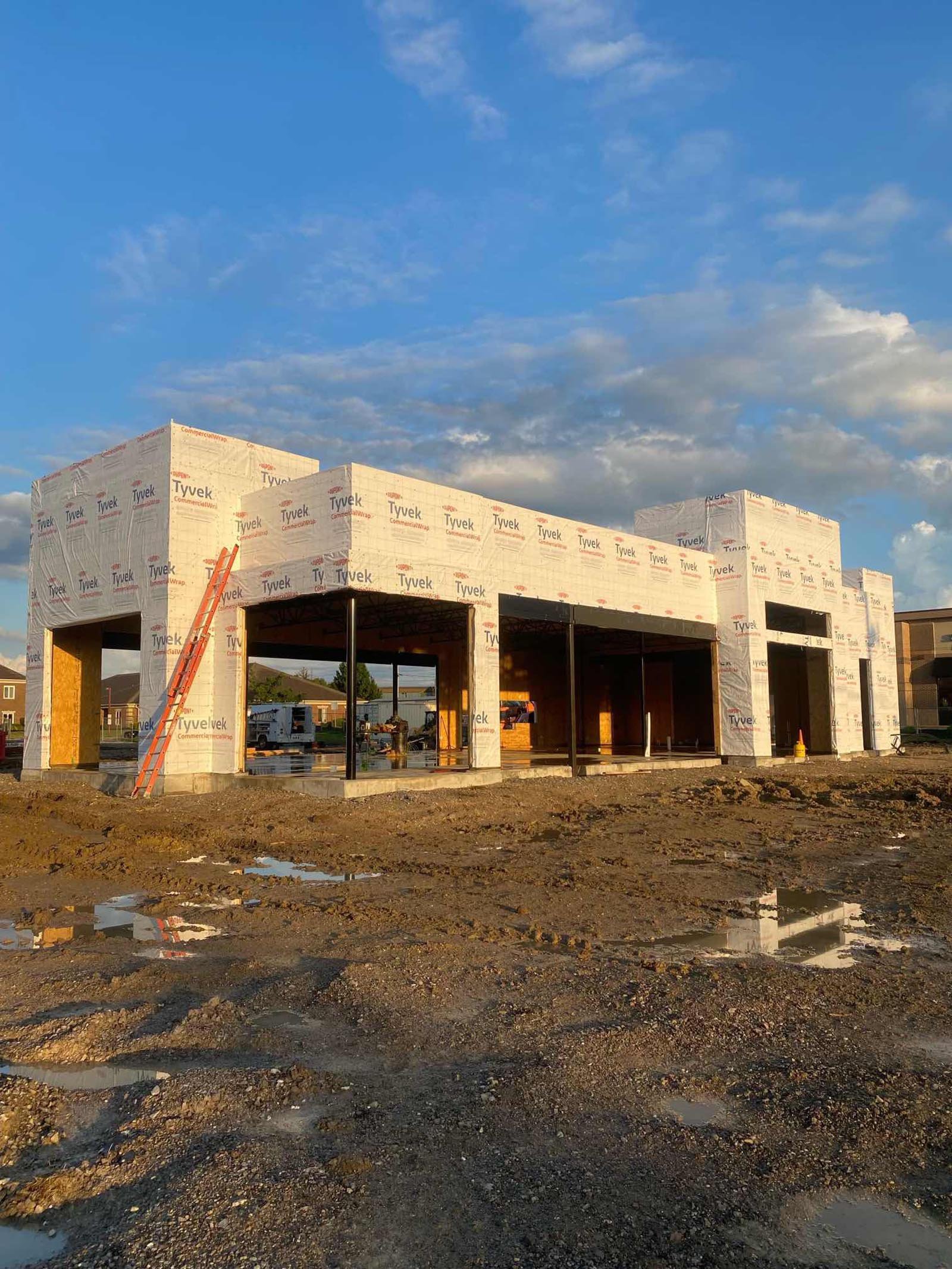
SIP erection is very similar to stick construction. Many standard carpentry tools are still used when building with SIPs, however power lifting equipment is required as a SIP can weigh up to 800 pounds. SIP screws are required for attaching SIPs together at corners or interior walls and fastening the roof down.
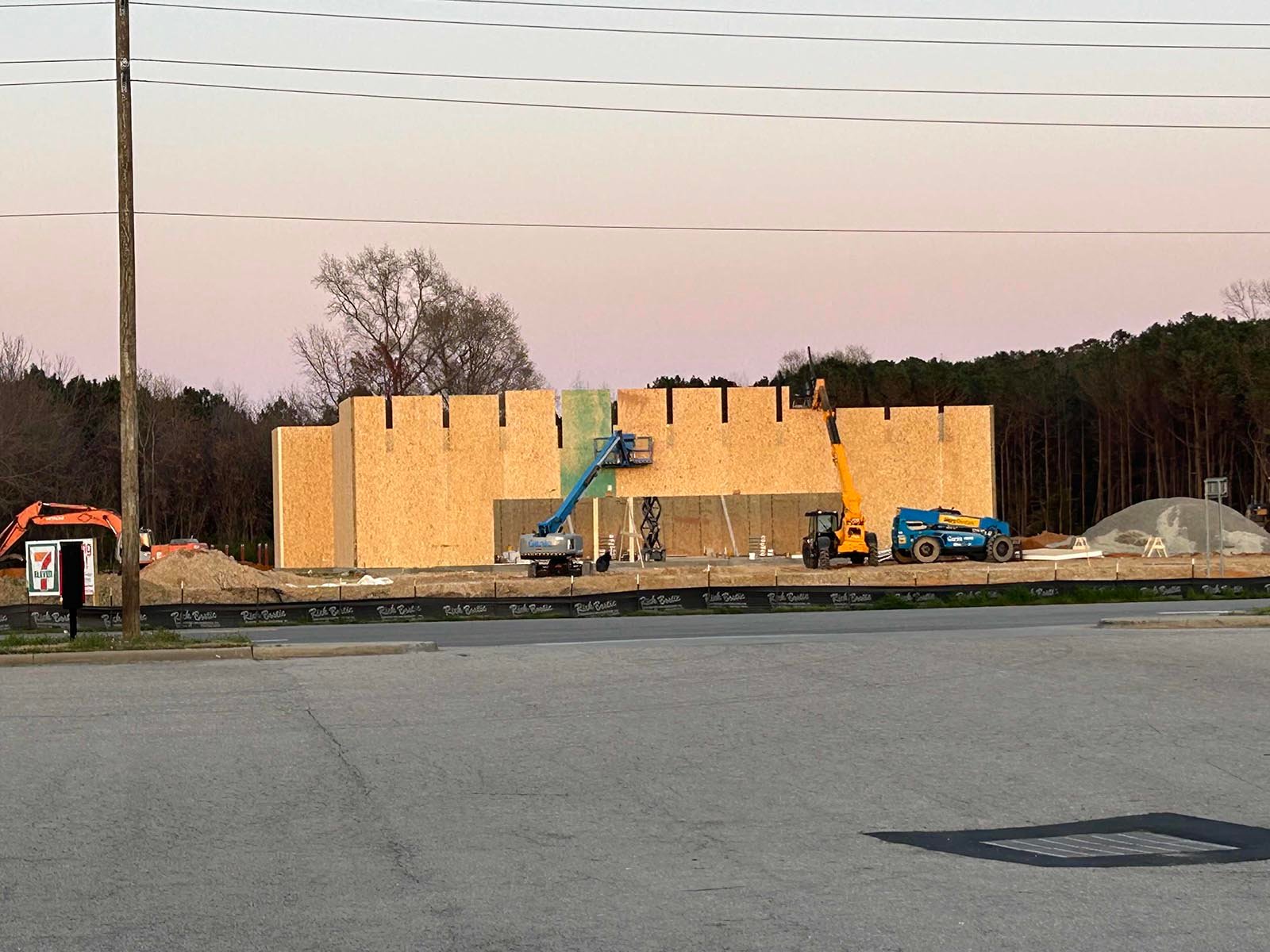
Installing a base plate for rough framing and installing a base plate for SIPs vary only slightly but in two important ways. With SIPs, the OSB faces carry the axial load and with stick-construction the studs carry the axial load. Since the faces or skins are load bearing, they must bear a structural member – usually a treated plate or a structural wood deck. Also, when using SIP walls on a concrete slab, a treated sill plate cut to the width of the panel thickness is required to separate the OSB face of the panel from the concrete slab. This is required to keep water from wicking through the concrete into the OSB and causing moisture damage.
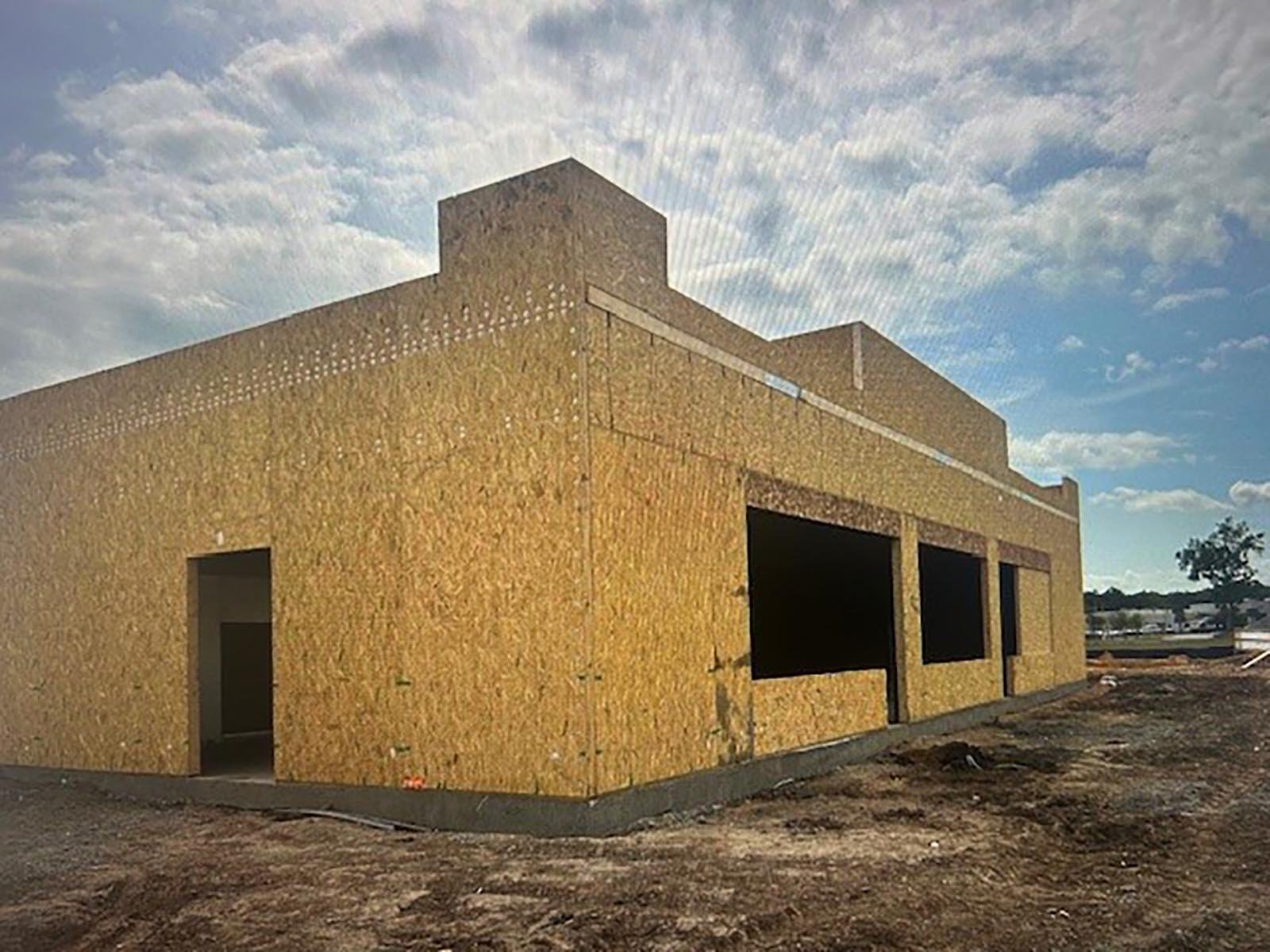
Designing with PorterSIPs
-
Best utilizing materials helps keep the cost of SIP projects as low as possible.
The standard 8’ x 24’ SIP size is determined by availability of “jumbo” OSB. The speed of construction offered by jumbo panels has resulted in the 8’ x 24’ size OSB becoming the SIP industry standard. The cost of a SIP project is partially dictated by the number of 8’ x 24’ sheets that are required.
-
Eight-foot-high wall panels can be up to 24’ long in a single piece and typically will utilize almost 100% of the available 8’ x 24’ material. When walls need to be taller than 8’, the direction of the panels will be turned 90° – in this scenario, there will be a spline joint at least every 8’, but the panels can be up to 24’ tall. In residential SIP construction today, 8’ x 9’ or 8’ x 10’ panels are very commonly used to achieve 9’-or 10’-tall walls. A designer should keep in mind that, in general, window openings that are less than 4’ wide can be achieved without using a header, again saving cost.
SIP walls can be engineered to meet most any loading including high wind loading. In general, SIPs are easier to use and engineer when high load capacities are required. For example, in South Florida, building with SIPs is significantly less expensive due to the number and size of hold-downs required for stick framed structures.
-
SIPs make cathedral ceilings easy to build and extremely energy efficient. Compared with rafter construction, they are more cost effective to install and much more energy efficient. Cathedral ceilings add instant height to a room and can negate the need for 9’ and 10’ tall wall panels. When planning to use SIPs in roof construction, it is important to note that a roof panel must span from one bearing support to another.
Construction support members can be ridge beams, bearing walls, rafters, purlins or trusses. If the design calls for hips or valleys, note that these edges usually need to be supported with valley beams or hip rafters. If the design of the building calls for horizontal ceilings, SIPs can be used as a ceiling panel, or SIPs can be installed at the roof line, and the horizontal ceiling can be constructed with ceiling joists. The best way to take advantage of SIPs’ inherent benefits is to design a cathedral ceiling into a building with a pitched roof. Using a SIP roof system in conjunction with SIP walls will offer much more energy efficiency than using SIP wall alone, or a SIP roof alone.
-
The least expensive way to build a well insulated enclosure is monoslope construction with SIPs. Buildings up to 20 feet wide with flat or shed roofs are ideal for this system. Buildings up to 40 feet wide can use a semi-monoslope construction with only columns and an interior beam down the center.
-
SIPs should not be used for interior floor systems because they are not as cost effective nor as accessible as conventional engineered wood truss or I joist systems. The easy access available in conventional engineered floor systems for plumbing, HVAC, and primary electrical is very important while thermal insulation between floors typically is not. SIP floors are best used whenever a floor needs to be insulated: over an unheated crawl-space, for a room that is elevated, or over any other unheated space. SIP floor systems frequently use engineered wood splines to increase the stiffness. Ask your local sales representative for more details.
-
Producing special shapes and compound cut panels is easy and accurate when you specify PorterSIPs. With SIP specific, three-dimensional CAD software, and 5-axis-capable CNC machinery, panels now fit much more precisely than ever before. Complicated dormers with gables, hips, and valley cuts can now be supplied as easily as smaller rectangular panels used to be. Special shapes like round-top windows can be accomplished with accuracy. Relying on skilled framing carpenters is less reliable than it used to be. With CNC-cut SIPs, the complicated cutting is done reliably and correctly in the factory.
-
Due to jumbo roof panels’ capacity for long spans, oftentimes, load bearing walls can be eliminated. Without load bearing walls, the interior space can be designed with an open concept and also can be more flexible as needs of the building change over time.
-
SIP juncture details have evolved and have been refined greatly over the last 15 years. These details result in a highly sealed enclosure. Preventing moisture and vapor penetration at junctures is extremely important. The resulting building envelope will enable you to install downsized heating and cooling systems. This tight envelope may also require an air-to-air heat exchanger to reduce the humidity. Contact your PorterSIPs sales representative to explain further.
Private label weather-resistant barrier
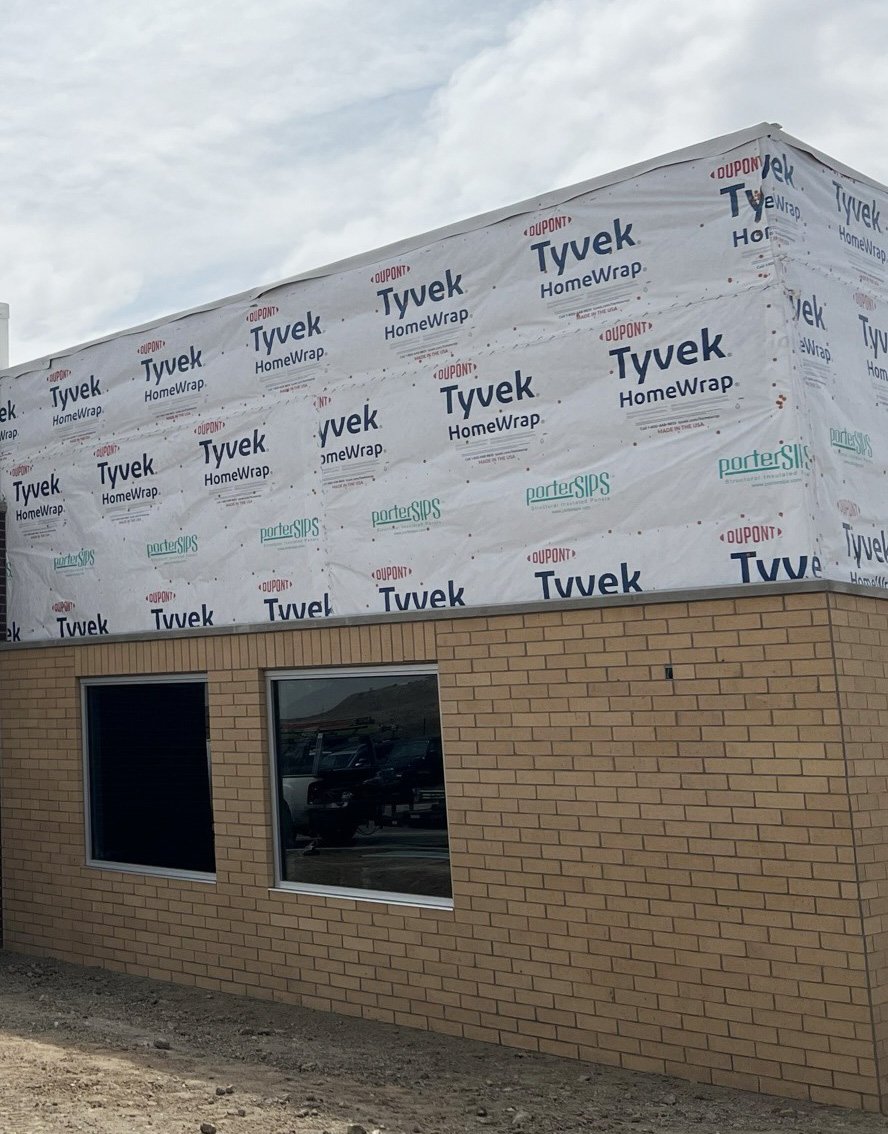
Private label sealant
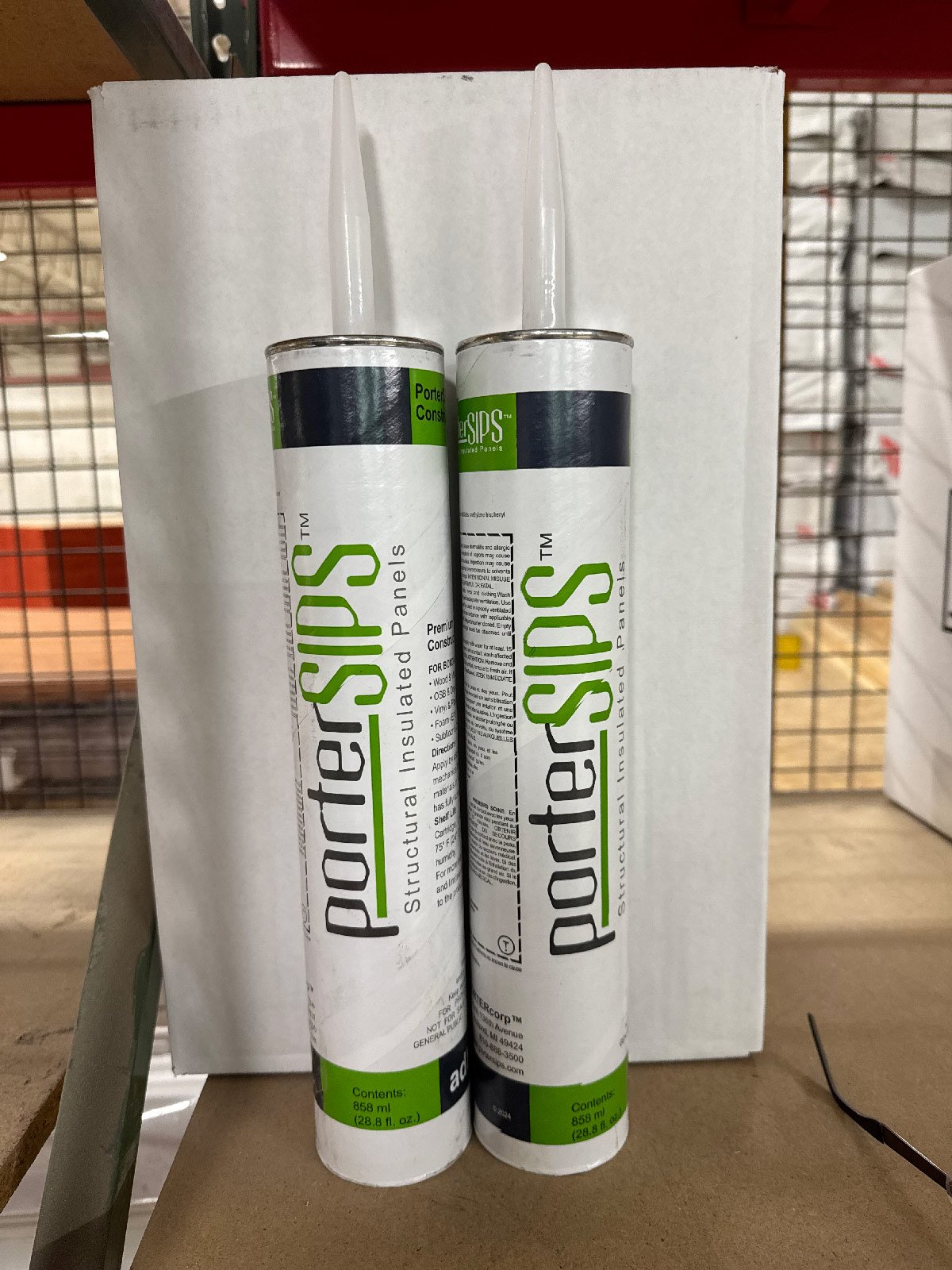