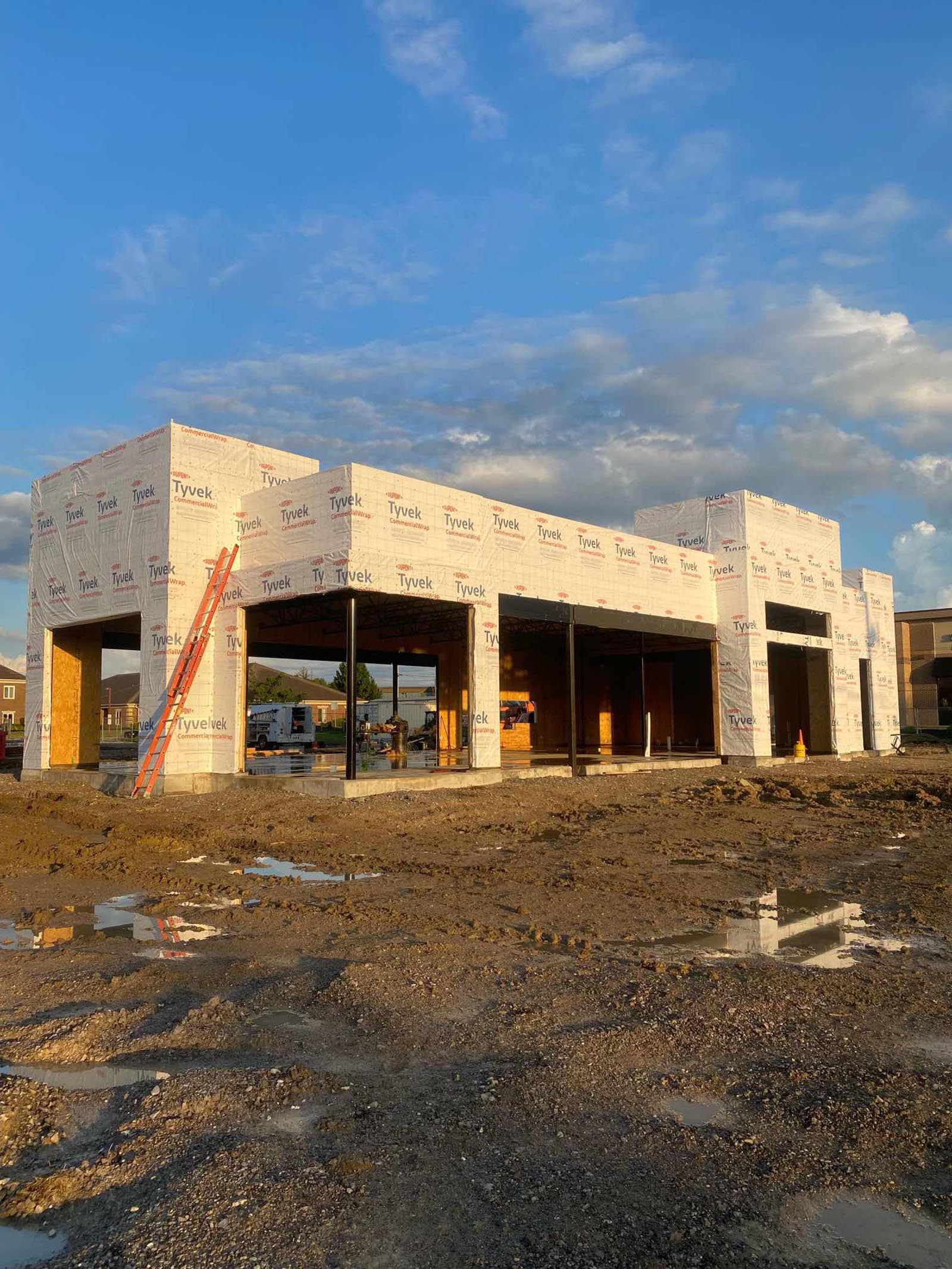
About Us
- Home
- About Us
About Us
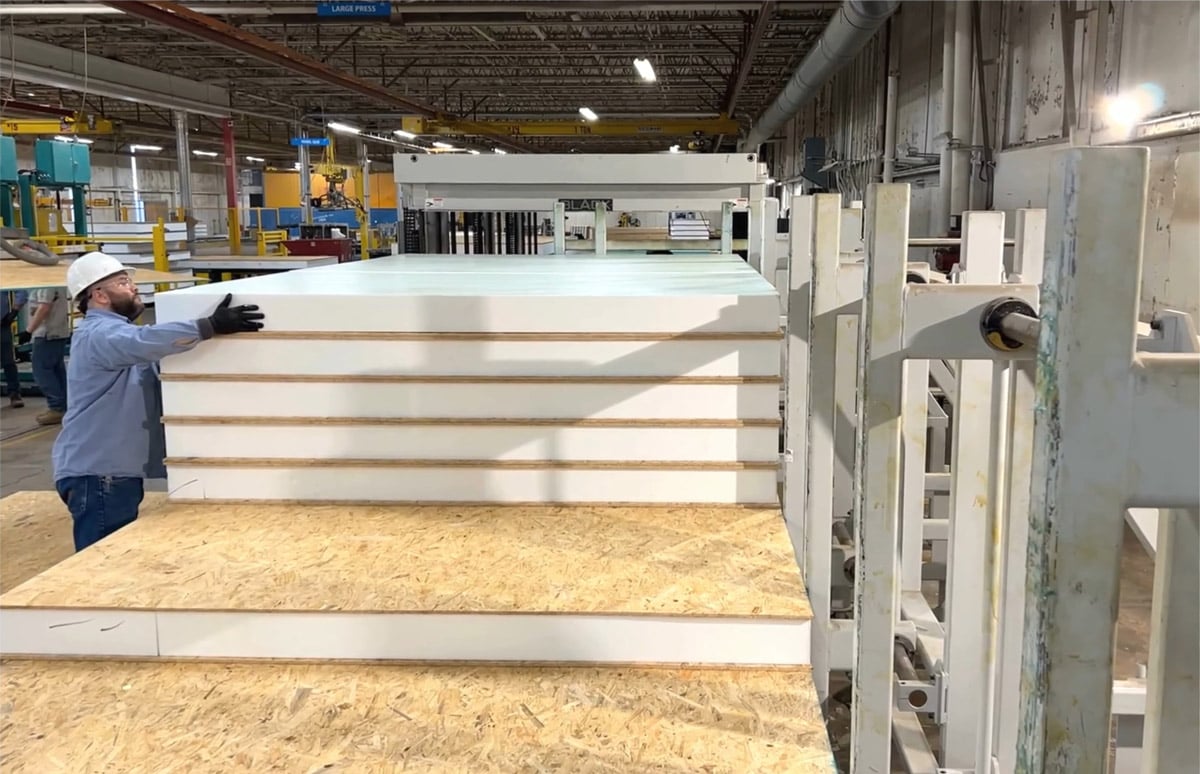
Porter Corp
The Porter Corp campus is home to over 131,000 square feet of manufacturing facilities, corporate offices, shelters, prototypes and R&D ventures. It is situated on 20 acres in Holland, Michigan. Porter Corp has state of the art SIPs manufacturing equipment and operations, which includes multiple CNC machines in flexible manufacturing cells. We are committed to serving customers well and exceeding their expectations.
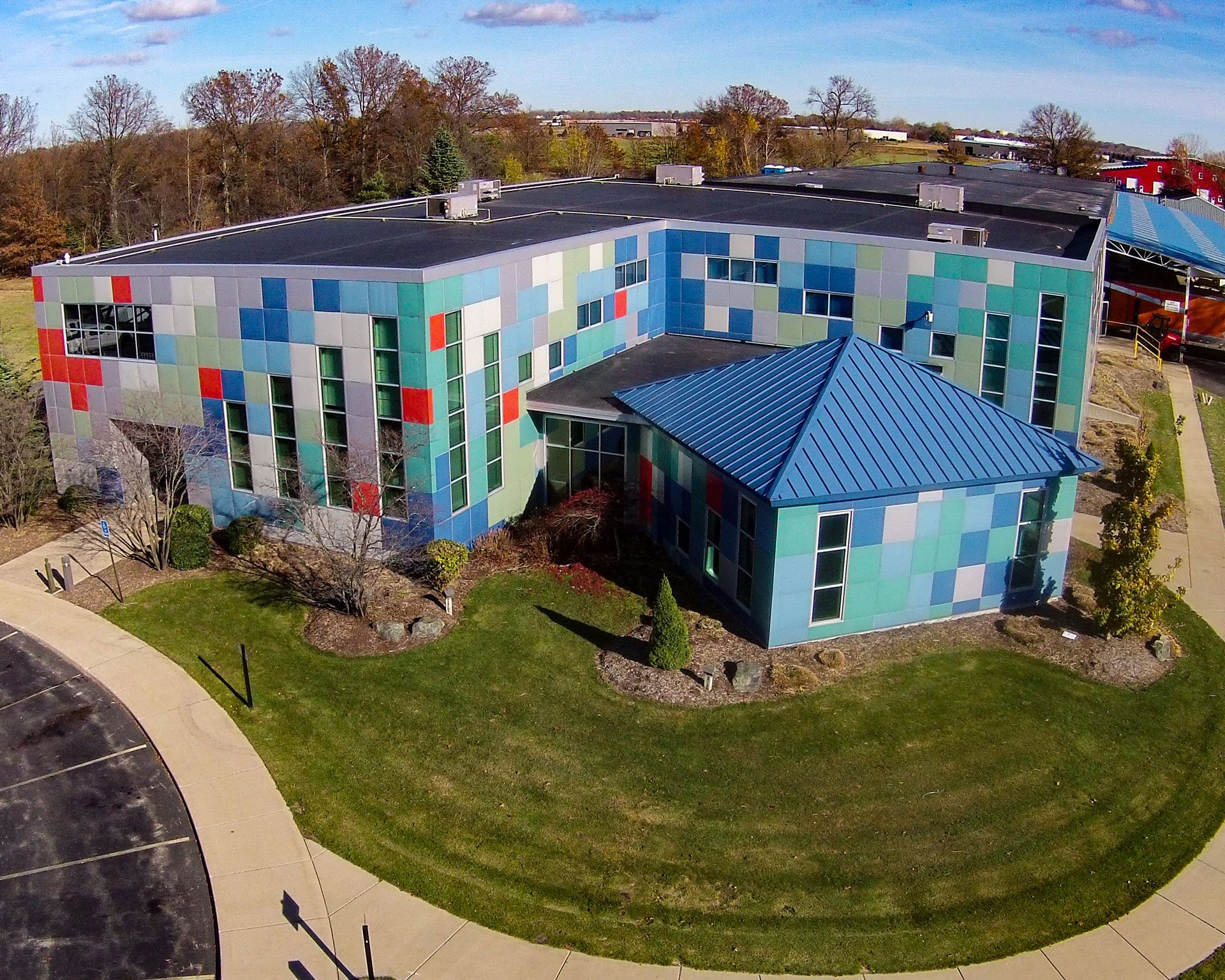
About Our Parent Company
PlayCore is a purpose-driven Company committed to building healthy communities around the world by advancing play and recreation. The company infuses scholarly learning, through its Center for Outreach, Research, and Education, into its comprehensive family of brands. PlayCore combines best-in-class educational programming with the most comprehensive portfolio of play and recreation products and services to create tailored environments that match the unique needs of each community served. Learn more at www.playcore.com
PlayCore’s Center for Outreach, Research, & Education (CORE) is committed to researching and advocating for the impact of play and recreation on a community’s vitality and why it’s valuable to invest in community health and wellness. In collaboration with leaders and scholars, CORE gathers and shares knowledge, through a variety of evidence-based resources and services, to positively advance diverse community needs.
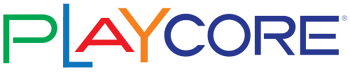
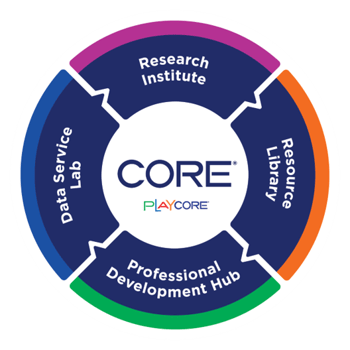